BGA Reballing
BEST’s Reballing Solution
BEST’s BGA reballing is a highly reliable, repeatable and proven process for changing solder alloy or restoring a part to its original specifications. Our process has been perfected over 20+ years of reballing BGAs for electronic manufacturers across the country. Our capabilities include handling a wide range of package sizes, ball counts and complex arrays to meet our customer’s needs. BEST’s reballing process follows industry specifications including IPC J-STD-001, IPC 7711, GEIA-STD 006 and IEC TS 62647-4.
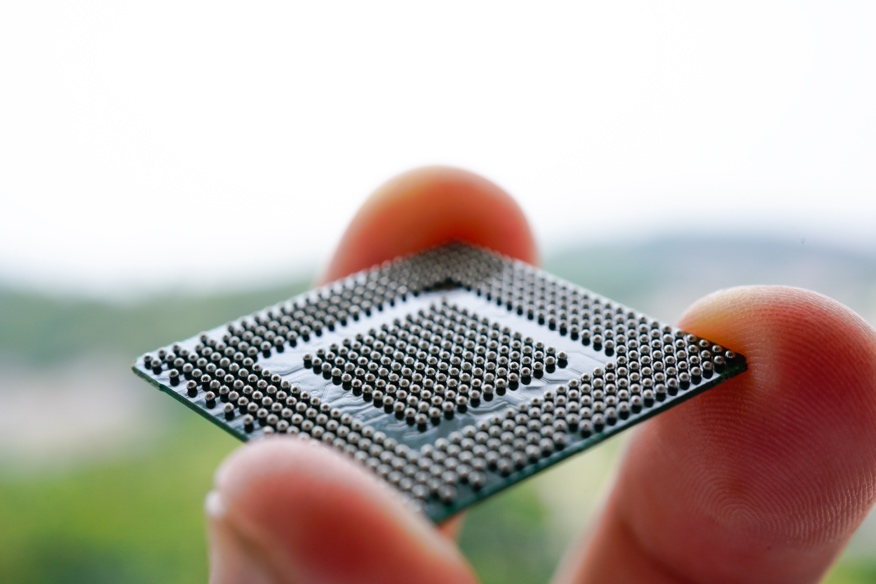
Commitment to Quality
We take great pride in providing the highest quality services to all our customer. Our quality comes from having highly trained operators, strict ESD compliance, MSD controls and exceptional quality control systems in place. When you work with BEST, you get a workmanship guarantee along with exceptional customer service, competitive pricing and expedited lead times.
Why Reball with BEST?
When it comes to reballing BGAs, there are many options out there to choose from. The BEST advantage comes from our years of reballing experience and our ability to make custom reballing preforms to fit nearly any package. By making preforms in-house, we can significantly reduce lead-times for our customers in both small and large volume jobs.
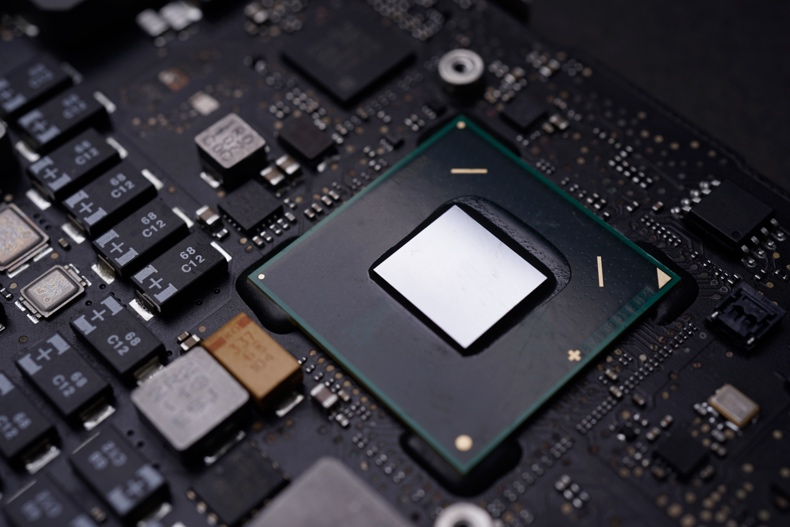
Reballing for Military and Aerospace
BEST has automated robotic deballing available in compliance with IEC TS 62647-4. This process uses a dynamic solder wave to remove the original solder balls in a touch-free manner. Material traceability, record retention and process qualification procedures are also in place to meet Military and Aerospace requirements for reballing.
Additional testing includes:
- XRF
- Scanned Acoustic Microscopy
- Ionic Cleanliness
- DPA
- X-ray
- Ball Shear
- Component marking services
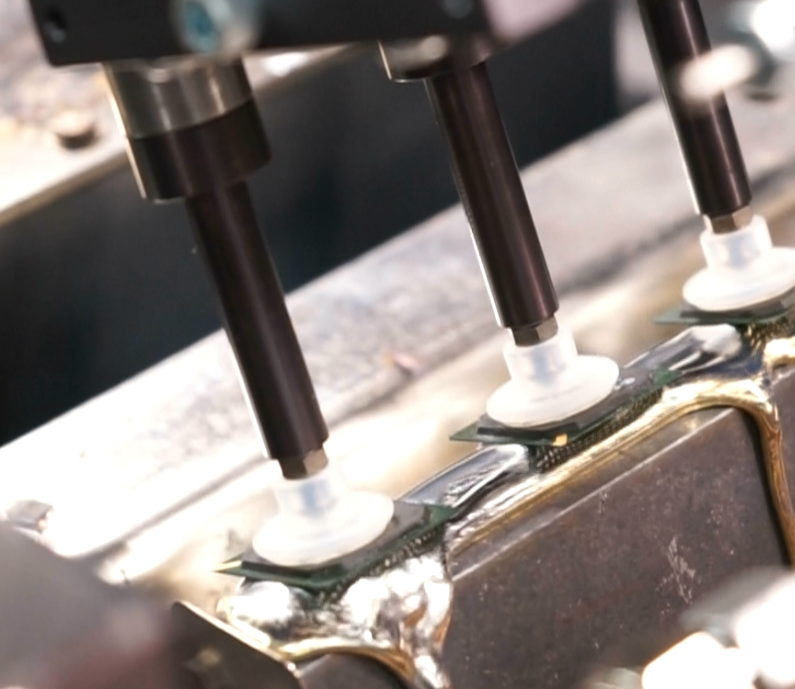
BEST Reballing Specifications
Package Sizes: 3 x 3mm to 60 x 60mm, ball count 4 to >8,000
Pitch: 0.20mm to 1.5mm
Ball sizes: 8 mils (203.2 μm) to 35 mils (889 μm)
Alloys: Sn63Pb37, SAC305, Sn90Pb10 (standard), other alloys, plastic core or solder-coated balls capable
Package Materials: Plastic, ceramic, metal
Conversions: Placing balls on bottom-terminated components (QFN, LGA)
Packaging: Tape and reel, matrix trays
Deballing Methods: solder braid/wick and automated robotic deballing via dynamic solder wave
Ball Attach Methods: EZReball™ reballing preforms-designed and manufactured in house or automated reballing equipment
Inspection: Visual and X-Ray inspection for shorts, bridges, ball sphericity, ball diameter.
Other Services: Dry Packing, Baking, XRF Testing, Scanned Acoustic Microscopy, Ionic Cleanliness, DPA, X-ray and Ball Shear Testing, Solderability Testing, Laser Component Marking, paint dot marking of various colors
Compliance RoHS, REACH, ITAR
Industry Standards:
ISO 9001 | GEIA-0006 |
J-STD-001 | NASA -STD-8739.2 |
IPC 7711 | IEC TS62647-4. |
ESD: Per ANSI/ESD S20.20 guidelines
MSL: Per IPC/JEDEC J-STD-033 guidelines
Typical lead times:
Small volumes: 3-5 business days
Medium volumes: 1-2 weeks
Large volumes: 2-6 weeks